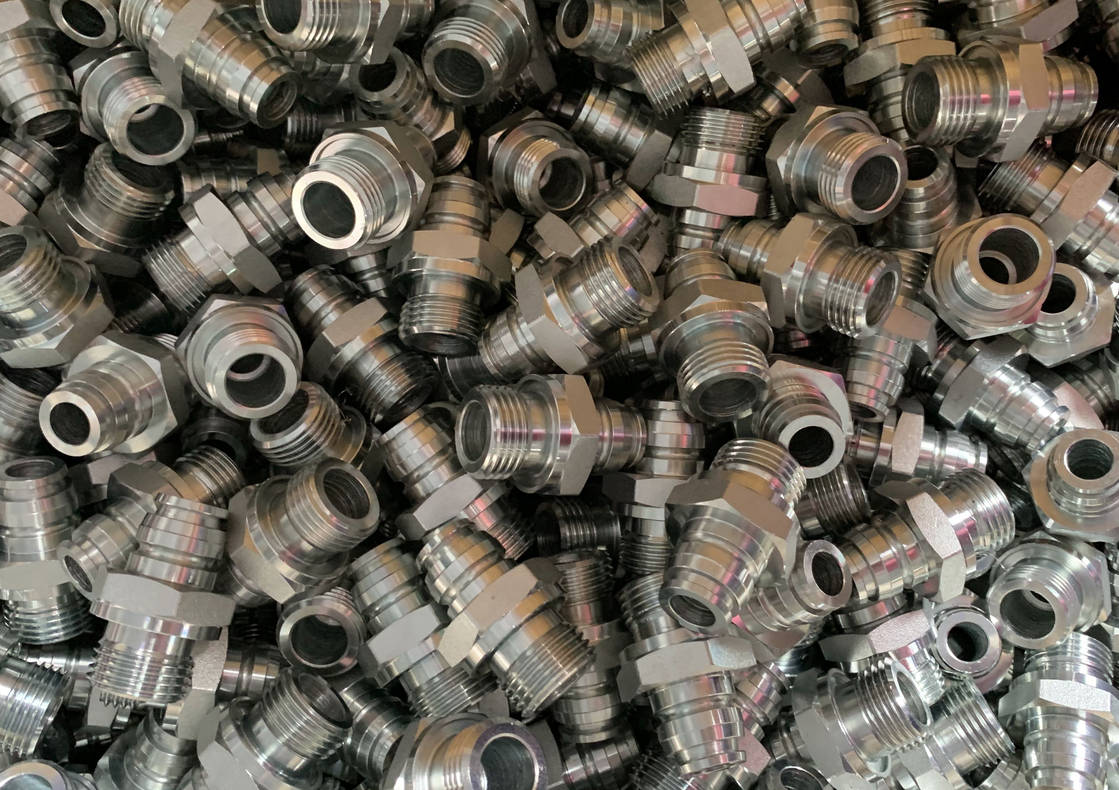
When sourcing hydraulic fittings, understanding the key quality indicators is crucial for ensuring optimal performance and safety. This article will explore five essential quality indicators that professionals should consider when selecting hydraulic fittings. Each indicator plays a significant role in the overall reliability of hydraulic systems, and being informed can help prevent costly mistakes and improve equipment efficiency. By focusing on these indicators, you’ll be better equipped to make informed sourcing decisions.
1. What Are Quality Indicators for Hydraulic Fittings?
Quality indicators for hydraulic fittings are specific criteria that assess the reliability and performance of these components. These indicators help determine whether a fitting is suitable for a particular application. But here’s the kicker—neglecting to consider these indicators can lead to serious operational issues, including leaks and system failures.
The five key quality indicators include material quality, dimensional accuracy, pressure rating, surface finish, and certifications. Each of these indicators plays a crucial role in ensuring that the fittings perform as expected under various conditions.
Material quality is fundamental, as it affects the fitting’s durability and resistance to corrosion. Dimensional accuracy ensures that fittings fit properly with other components, preventing leaks. Pressure ratings indicate the maximum pressure a fitting can withstand without failure. Surface finish impacts the fitting’s ability to create a reliable seal. Finally, certifications provide assurance that the fittings meet industry standards for safety and performance.
Understanding these quality indicators allows professionals to make informed decisions when sourcing hydraulic fittings, ultimately leading to more reliable and efficient systems.
Quality Indicator | Importance | Impact |
---|---|---|
Material Quality | Affects durability and corrosion resistance | Prevents premature failure |
Dimensional Accuracy | Ensures proper fit | Reduces leaks and maintenance |
Pressure Rating | Indicates maximum pressure capacity | Ensures safety under operating conditions |
Surface Finish | Impacts sealing ability | Prevents leaks and enhances performance |
Certifications | Confirms compliance with standards | Ensures reliability and safety |
2. Why Is Material Quality Crucial in Hydraulic Fittings?
Material quality is one of the most critical indicators when it comes to hydraulic fittings. What’s the real story? The materials used in fittings directly affect their performance, durability, and resistance to environmental factors.
Hydraulic fittings are commonly made from materials such as stainless steel, brass, and aluminum. Each material has its unique properties that make it suitable for specific applications. For instance, stainless steel fittings are known for their exceptional corrosion resistance, making them ideal for use in environments exposed to moisture or chemicals. On the other hand, brass fittings provide excellent durability and are often used in less demanding applications.
When sourcing hydraulic fittings, it’s essential to consider the operating environment and the fluids that will be transported through the system. For example, if the fittings will be exposed to aggressive chemicals, selecting a material with high chemical resistance is paramount. Failing to choose the right material can result in premature wear, leaks, and system failures, leading to costly repairs and downtime.
Furthermore, the manufacturing process also plays a vital role in material quality. High-quality fittings undergo stringent testing and inspection to ensure they meet the required specifications. This rigorous quality control helps guarantee that the fittings will perform reliably under the stresses of hydraulic applications.
Material | Properties | Ideal Applications |
---|---|---|
Stainless Steel | Corrosion-resistant, durable | Harsh environments, chemical exposure |
Brass | Strong, good corrosion resistance | General-purpose applications |
Aluminum | Lightweight, moderate strength | Low-pressure systems, weight-sensitive applications |
3. How Does Dimensional Accuracy Impact Fitting Performance?
Dimensional accuracy is a vital quality indicator that directly affects the performance of hydraulic fittings. Ready for the good part? Properly dimensioned fittings ensure a secure and leak-free connection between components, which is essential for maintaining system integrity.
Hydraulic fittings come in various types and sizes, and each fitting must meet specific dimensional standards to ensure compatibility. When fittings are manufactured with precise dimensions, they fit correctly with hoses, pipes, and other components, preventing leaks and pressure losses. Conversely, fittings that do not meet dimensional specifications can lead to gaps in connections, resulting in fluid leakage and reduced system efficiency.
Moreover, dimensional accuracy is crucial when dealing with high-pressure hydraulic systems. In these applications, even the slightest deviation from the specified dimensions can compromise the fitting’s ability to withstand pressure, potentially leading to catastrophic failures. Therefore, it’s essential to source fittings from manufacturers who adhere to strict dimensional standards and perform regular quality checks during production.
In addition to preventing leaks, accurate dimensions facilitate easier installation and maintenance. When fittings fit properly, technicians can assemble and disassemble systems more efficiently, reducing downtime during maintenance tasks.
Dimensional Aspect | Importance | Consequence of Inaccuracy |
---|---|---|
Sizes | Ensures proper fit | Risk of leaks and failures |
Thread Specifications | Promotes secure connections | Compromised system safety |
Tolerances | Allows for seamless integration | Increased maintenance costs |
4. What Role Does Pressure Rating Play in Quality Assessment?
Pressure rating is a fundamental quality indicator for hydraulic fittings, determining the maximum pressure the fitting can safely withstand during operation. This is where it gets interesting—understanding pressure ratings is crucial for ensuring the safety and reliability of hydraulic systems.
Each hydraulic fitting is designed to operate within specific pressure limits. These limits are determined by the materials used in the fittings and their construction. When sourcing fittings, it’s essential to choose ones that have pressure ratings exceeding the maximum pressure your system will encounter. Failing to do so can result in catastrophic failures, leaks, and potential hazards.
For example, in industrial applications where pressures can fluctuate dramatically, selecting fittings with higher pressure ratings provides an added safety margin. This ensures that even during peak operational conditions, the fittings will not fail. Conversely, using fittings with inadequate pressure ratings can lead to premature failure, resulting in costly repairs and downtime.
It’s also important to consider the type of hydraulic fluid being used, as certain fluids can affect the fitting’s performance under pressure. For instance, fluids with high viscosity may require fittings that can withstand more significant pressure variations. Understanding the specific requirements of your hydraulic system will help you choose the appropriate fittings and ensure optimal performance.
Pressure Rating | Definition | Importance |
---|---|---|
Maximum Allowable Pressure | Highest pressure a fitting can handle | Prevents leaks and failures |
Burst Pressure | Pressure at which a fitting fails | Indicates safety limits |
Working Pressure | Normal operating pressure | Guides selection of appropriate fittings |
5. Why Is Surface Finish Important for Hydraulic Fittings?
Surface finish is a critical quality indicator that directly influences the performance and reliability of hydraulic fittings. So, what’s the deal? The surface finish of a fitting affects its sealing capabilities and resistance to corrosion, which are essential for maintaining system integrity.
A smooth surface finish allows for better sealing between the fitting and the connected components. When fittings have rough or uneven surfaces, they are more likely to create gaps that can lead to leaks. This is particularly important in high-pressure applications where even a small leak can result in significant fluid loss and reduced system efficiency.
Additionally, a good surface finish enhances the fitting’s resistance to corrosion. Hydraulics systems often operate in environments exposed to moisture, chemicals, and other corrosive agents. Fittings with a high-quality surface finish are less susceptible to corrosion, extending their lifespan and maintaining performance over time.
Standards for acceptable surface finishes vary depending on the application. For example, fittings used in food processing or pharmaceutical industries may require smoother finishes to meet hygiene standards. Conversely, industrial applications may prioritize functional performance over aesthetic considerations. Regardless of the application, it’s essential to ensure that the surface finish of hydraulic fittings meets the necessary specifications.
Surface Finish Type | Description | Importance |
---|---|---|
Smooth Finish | Minimal surface roughness | Enhances sealing and prevents leaks |
Coated Finish | Protective coatings for corrosion resistance | Extends lifespan in harsh environments |
Rough Finish | Textured surface for certain applications | May be suitable for specific industrial uses |
6. How Do Certifications and Standards Ensure Quality?
Certifications and standards play a crucial role in ensuring the quality and safety of hydraulic fittings. What’s the catch? By adhering to recognized certifications, manufacturers demonstrate their commitment to producing reliable and compliant products.
Industry certifications, such as ISO, SAE, and DIN, establish benchmarks for quality and performance in hydraulic fittings. When a fitting is certified, it indicates that it has undergone rigorous testing and meets specific criteria set by these organizations. This assurance allows engineers and technicians to trust that the fittings they are using will perform as expected under various conditions.
For instance, ISO certifications focus on international quality standards, ensuring that fittings are compatible and reliable across different markets. SAE standards, on the other hand, emphasize performance specifications particularly relevant to automotive applications. DIN standards are recognized in Europe and prioritize quality and safety in hydraulic components.
When sourcing hydraulic fittings, it’s essential to look for products that carry these certifications. This not only provides peace of mind regarding the product’s performance but also helps maintain compliance with industry regulations. Additionally, manufacturers that prioritize certification often implement comprehensive quality control processes, further enhancing the reliability of their products.
Certification | Organization | Benefits |
---|---|---|
ISO | International Organization for Standardization | Global compatibility and reliability |
SAE | Society of Automotive Engineers | Performance specifications for automotive applications |
DIN | Deutsches Institut für Normung | Quality and safety standards in Europe |
7. What Testing Methods Are Used to Assess Hydraulic Fitting Quality?
Testing methods are essential for assessing the quality of hydraulic fittings. This is where it gets interesting—rigorous testing ensures that fittings will perform reliably under specified conditions. Various testing methods are employed to evaluate different aspects of hydraulic fittings.
One common testing method is pressure testing, where fittings are subjected to pressures greater than their rated maximum to assess their integrity. This method helps identify potential leaks and weaknesses in the fittings before they are installed in hydraulic systems. Another important test is the burst pressure test, which measures the maximum pressure a fitting can withstand before failing. This is crucial for determining the safety limits of the fittings.
Additionally, dimensional checks are conducted to ensure that the fittings meet specified tolerances and standards. These checks help confirm that the fittings will fit properly with other components, preventing leaks and ensuring optimal performance.
Material tests, such as tensile strength and corrosion resistance tests, are also critical in evaluating the quality of hydraulic fittings. These tests assess the materials used in fittings to ensure they can withstand the operating conditions they will encounter in real-world applications.
Testing Method | Purpose | Importance |
---|---|---|
Pressure Testing | Assess integrity under pressure | Identifies leaks and weaknesses |
Burst Pressure Test | Determine maximum pressure capacity | Ensures safety limits |
Dimensional Checks | Verify compliance with specifications | Prevents leaks and ensures proper fit |
8. How Can You Evaluate Supplier Reputation and Reliability?
Evaluating supplier reputation and reliability is a crucial step in sourcing hydraulic fittings. So, how do you determine if a supplier can meet your quality standards? Here are some effective strategies.
First, research the supplier’s history and experience in the industry. A supplier with a long-standing presence and a proven track record is more likely to provide high-quality products. Look for testimonials and case studies from previous customers to gauge the supplier’s reliability. Positive reviews and experiences from other businesses can provide valuable insights into the supplier’s performance.
Next, assess the supplier’s certifications and quality assurance processes. Reputable suppliers will often hold relevant industry certifications, indicating their commitment to quality and compliance. Ask for documentation that demonstrates their adherence to quality standards, such as ISO or SAE certifications.
Additionally, consider the level of customer support the supplier offers. A reliable supplier should be responsive and willing to provide assistance with questions, concerns, or issues that may arise. Good communication is essential for maintaining a successful business relationship and ensuring that you receive the support you need.
Finally, consider visiting the supplier’s facilities if possible. A firsthand look at their operations can provide insights into their manufacturing processes, quality control measures, and overall capabilities. This due diligence can help ensure that you are partnering with a reputable supplier.
Evaluation Method | Description | Benefit |
---|---|---|
Supplier History | Research years in business and experience | Indicates reliability and quality |
Certifications | Verify adherence to industry standards | Ensures compliance and quality assurance |
Customer Support | Assess responsiveness and assistance | Facilitates better business relationships |
9. What Are the Common Mistakes to Avoid When Sourcing Fittings?
When sourcing hydraulic fittings, there are several common mistakes that can lead to costly issues. Understanding these pitfalls is essential for making informed decisions. What’s the catch? By avoiding these mistakes, you can enhance the reliability of your hydraulic systems.
One significant mistake is focusing solely on price rather than quality. While it may be tempting to choose the cheapest options, low-quality fittings can lead to failures and increased maintenance costs. Always prioritize quality indicators such as material, dimensional accuracy, and certifications over price alone.
Another common error is neglecting to verify supplier credentials. Failing to conduct due diligence on suppliers can result in sourcing substandard fittings. Ensure that you research suppliers thoroughly, looking for reviews, certifications, and industry reputation before making a purchase.
Ignoring compatibility is another mistake that can have severe consequences. When fittings are incompatible with hoses, pipes, or other components, it can lead to leaks and system failures. Always confirm that the fittings you choose meet the specifications required for your hydraulic system.
Finally, many professionals overlook the importance of maintaining clear records of fittings used in their systems. Keeping documentation of fitting specifications, certifications, and maintenance history is crucial for ensuring compliance and tracking performance over time.
Common Mistake | Description | Consequence |
---|---|---|
Focusing on Price | Choosing fittings based solely on cost | Increased maintenance costs and failures |
Neglecting Supplier Verification | Failing to research supplier credentials | Sourcing substandard fittings |
Ignoring Compatibility | Not confirming fitting specifications | Leaks and system failures |
10. How to Implement a Quality Assurance Process for Sourcing?
Implementing a quality assurance process for sourcing hydraulic fittings is essential for ensuring that your components meet the necessary standards. What’s the real story? A well-defined quality assurance process can help you maintain high-quality standards and reduce the risk of failures.
Start by creating a quality assurance checklist that outlines the key quality indicators you will evaluate when sourcing fittings. This checklist should include items such as material quality, dimensional accuracy, pressure ratings, surface finish, and certifications. Having a clear set of criteria will guide your sourcing decisions and help ensure consistency.
Next, establish relationships with reputable suppliers who prioritize quality. Communicate your quality standards and expectations to suppliers, and verify that they can meet these requirements. Regularly review supplier performance and provide feedback to ensure ongoing compliance with your quality assurance process.
Additionally, consider conducting regular audits of your sourcing process. Evaluate how well your quality assurance measures are being implemented and identify areas for improvement. This proactive approach will help you maintain high standards and ensure that your hydraulic systems operate reliably.
Finally, train your team on the importance of quality assurance in sourcing fittings. Ensure that all personnel involved in the sourcing process understand the quality indicators and the significance of adhering to them. This training will foster a culture of quality within your organization.
Quality Assurance Step | Description | Importance |
---|---|---|
Create Checklist | Outline key quality indicators | Guides sourcing decisions |
Establish Supplier Relationships | Ensure quality standards are met | Maintains consistent quality |
Conduct Audits | Evaluate sourcing process effectiveness | Identifies areas for improvement |
11. What Are the Benefits of Using High-Quality Hydraulic Fittings?
Investing in high-quality hydraulic fittings offers numerous benefits that can enhance the overall efficiency and reliability of hydraulic systems. So, what’s the scoop? Understanding these benefits can motivate you to prioritize quality in your sourcing decisions.
First, high-quality fittings are more durable and resistant to wear and tear. This durability leads to fewer failures and lower maintenance costs over time. In high-pressure applications, reliable fittings can prevent leaks, contributing to overall system efficiency and reducing the risk of catastrophic failures.
Moreover, using quality fittings enhances safety in hydraulic systems. Low-quality fittings are more likely to fail under pressure, posing risks to operators and equipment. High-quality fittings undergo rigorous testing and comply with industry standards, providing assurance that they will perform safely and effectively.
Additionally, high-quality fittings can improve system performance. When fittings are designed and manufactured to meet strict specifications, they facilitate better flow and pressure management within hydraulic systems. This improved performance can lead to enhanced productivity and operational efficiency.
Finally, investing in high-quality fittings contributes to long-term cost savings. Although the initial investment may be higher, the reduced maintenance and repair costs, combined with increased system reliability, ultimately lead to significant savings over time.
Benefit | Description | Impact |
---|---|---|
Durability | Fewer failures and lower maintenance costs | Increases system reliability |
Safety | Reduced risk of catastrophic failures | Protects operators and equipment |
Performance | Improved flow and pressure management | Enhances productivity |
12. How Do Environmental Factors Affect Fitting Quality?
Environmental factors play a significant role in determining the quality and performance of hydraulic fittings. This is where it gets interesting—considering these factors is essential for ensuring that fittings perform reliably under various conditions.
Temperature fluctuations can significantly impact hydraulic fittings. Extreme temperatures can cause materials to expand or contract, which may compromise the integrity of the fittings. When sourcing fittings, it’s essential to select those that are rated for the specific temperature ranges they will encounter in your application.
Chemical exposure is another critical factor to consider. Hydraulic fittings often operate in environments where they may be exposed to aggressive chemicals, oils, or other corrosive substances. Choosing materials that offer high resistance to these chemicals is vital for maintaining the integrity of the fittings and preventing premature failure.
Additionally, the location of the hydraulic system can influence the selection of fittings. Outdoor applications may expose fittings to harsh weather conditions, including rain, snow, and UV radiation. Selecting fittings that are specifically designed for outdoor use can help mitigate these risks and extend the lifespan of the components.
Environmental Factor | Impact | Consideration |
---|---|---|
Temperature | Affects material integrity | Choose fittings rated for temperature variations |
Chemical Exposure | Can degrade materials | Select fittings with chemical resistance |
Location | Outdoor conditions may cause damage | Use outdoor-rated fittings |
13. What Innovations Are Shaping the Future of Hydraulic Fittings?
The hydraulic fitting industry is constantly evolving, with new innovations emerging to enhance performance and safety. What’s the catch? Staying informed about these innovations can give you a competitive edge in your operations.
One of the most significant trends is the development of advanced materials for hydraulic fittings. Manufacturers are increasingly using high-strength polymers and composites that offer superior corrosion resistance and reduced weight. These materials can improve the performance of hydraulic systems, especially in demanding environments where traditional metals may fail.
Another important innovation is the integration of smart technology into hydraulic fittings. Smart fittings equipped with sensors can monitor pressure, temperature, and fluid levels in real-time. This data can be invaluable for optimizing system performance and enabling proactive maintenance, ultimately reducing the risk of failures.
Additionally, there is a growing emphasis on sustainability in the hydraulic fitting industry. Manufacturers are adopting environmentally friendly practices, such as using recyclable materials and reducing waste during production. This shift not only benefits the environment but also aligns with the increasing demand for sustainable products in various industries.
Innovation | Description | Impact |
---|---|---|
Advanced Materials | Use of high-strength polymers and composites | Enhanced performance and corrosion resistance |
Smart Technology | Fittings with built-in sensors | Real-time monitoring for optimization |
Sustainability | Adoption of eco-friendly practices | Aligns with market demand for sustainable products |
14. How to Stay Informed About Quality Standards and Trends?
Staying informed about quality standards and trends in hydraulic fittings is essential for maintaining compliance and ensuring optimal performance. So, what are the best ways to keep up with industry developments?
One effective method is to subscribe to industry publications and newsletters. Many organizations, including ISO, SAE, and DIN, provide regular updates on changes to standards and best practices. These publications often feature articles, case studies, and expert insights that can enhance your understanding of the industry.
Another useful approach is to attend industry conferences and seminars. These events often feature presentations from experts who discuss the latest trends, technologies, and standards in hydraulic fittings. Networking with peers at these events can also provide valuable insights and resources.
Finally, consider joining professional associations related to hydraulic systems. Membership in these organizations often provides access to exclusive resources, including research papers, webinars, and training materials. Being part of a professional network can help you stay informed about changes in standards and connect with industry experts.
Information Source | Description | Benefit |
---|---|---|
Industry Publications | Subscribe to newsletters and journals | Stay updated on changes and best practices |
Conferences | Attend seminars and networking events | Gain insights from experts and peers |
Professional Associations | Join industry-related groups | Access exclusive resources and training |
15. What Are Common Questions About Hydraulic Fitting Standards?
As hydraulic fitting standards play a crucial role in the industry, it’s natural to have questions about their implications and applications. Here are some common inquiries professionals may have.
Understanding these questions can help clarify the significance of hydraulic fitting standards and their relevance to your operations.
Question | Answer |
---|---|
What are hydraulic fitting standards? | Hydraulic fitting standards are guidelines that ensure compatibility, safety, and reliability of hydraulic components. |
How does the ISO standard work? | The ISO standard provides specifications for hydraulic fittings, ensuring they meet certain safety and performance criteria for global compatibility. |
What is the SAE standard for hydraulic fittings? | The SAE standard outlines specifications and performance criteria for hydraulic fittings used primarily in automotive and industrial applications. |
What is the DIN standard for hydraulic fittings? | The DIN standard establishes technical specifications for hydraulic fittings, focusing on quality and compatibility within European markets. |
How do I choose the right standard for my application? | Consider factors such as system requirements, component compatibility, and consulting with industry experts to select the appropriate standard for your hydraulic fittings. |
Conclusion
In conclusion, understanding hydraulic fitting standards is vital for ensuring the safety and reliability of hydraulic systems. By exploring the five essential quality indicators when sourcing hydraulic fittings, you can make informed decisions that enhance your operations. Each indicator serves a unique purpose, and adhering to these guidelines can help prevent costly failures and ensure optimal performance. Prioritize quality, stay informed about changes, and leverage these standards to achieve greater efficiency and reliability in your hydraulic systems.
FAQ Section
Q1: What are hydraulic fitting standards?
Hydraulic fitting standards are guidelines that ensure compatibility, safety, and reliability of hydraulic components.
Q2: How does the ISO standard work?
The ISO standard provides specifications for hydraulic fittings, ensuring they meet certain safety and performance criteria for global compatibility.
Q3: What is the SAE standard for hydraulic fittings?
The SAE standard outlines specifications and performance criteria for hydraulic fittings used primarily in automotive and industrial applications.
Q4: What is the DIN standard for hydraulic fittings?
The DIN standard establishes technical specifications for hydraulic fittings, focusing on quality and compatibility within European markets.
Q5: How do I choose the right standard for my application?
Consider factors such as system requirements, component compatibility, and consulting with industry experts to select the appropriate standard for your hydraulic fittings.