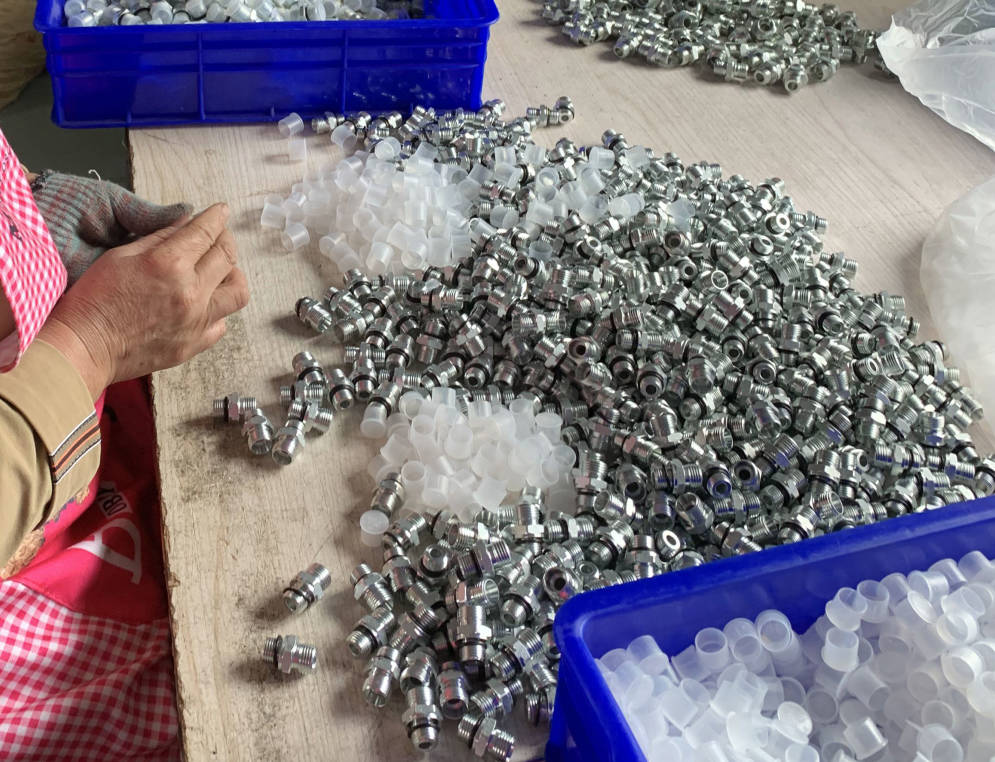
When it comes to sourcing hydraulic fittings, small businesses often face unique challenges. Understanding cost-effective strategies for hydraulic fitting procurement is vital for maintaining operational efficiency and managing expenses. This article will discuss essential techniques that small businesses can implement to source hydraulic fittings effectively without sacrificing quality. From leveraging supplier relationships to understanding material costs, this guide aims to equip you with the knowledge necessary to enhance your procurement strategies.
1. Why Does Material Selection Matter in Hydraulic Fitting Procurement?
Material selection is a pivotal factor in hydraulic fitting procurement that can significantly impact both performance and durability. But here’s the kicker—making the wrong choice can lead to operational inefficiencies and increased costs.
The materials used in hydraulic fittings must withstand specific conditions such as pressure and fluid type. For example, stainless steel is highly regarded for its corrosion resistance and strength, making it an excellent choice for applications in harsh environments. On the other hand, brass fittings, while often more affordable, may not offer the same level of durability under extreme conditions.
Choosing the right material also affects the long-term costs associated with maintenance and replacement. High-quality materials may have a higher initial cost but can lead to savings over time by reducing the frequency of repairs and replacements. Therefore, small businesses must carefully evaluate their specific operational needs and choose materials that align with both performance requirements and budget constraints.
Additionally, material selection can influence the overall efficiency of hydraulic systems. Reliable fittings that perform well can enhance fluid flow and reduce the risk of leaks, leading to improved system productivity. By prioritizing material selection in procurement processes, small businesses can create more efficient and reliable hydraulic systems that contribute to their overall success.
Material Type | Properties | Applications |
---|---|---|
Stainless Steel | High corrosion resistance, strength | Harsh environments, chemical exposure |
Brass | Good corrosion resistance, cost-effective | General applications, low pressure |
Aluminum | Lightweight, moderate strength | Low-pressure systems, weight-sensitive applications |
2. What Types of Materials Are Commonly Used in Hydraulic Fittings?
Hydraulic fittings are crafted from a range of materials, each offering distinct advantages and disadvantages. What’s the real story? Understanding these materials is essential for making informed decisions in the procurement process.
Stainless steel is a leading choice due to its superior resistance to corrosion and high strength. This material is particularly suitable for applications exposed to moisture or chemicals. For instance, in chemical processing industries, stainless steel fittings are essential for preventing failures caused by environmental exposure.
Brass fittings are also widely used, appreciated for their good corrosion resistance and affordability. They are commonly employed in low-pressure applications and general-purpose hydraulic systems. However, while brass is versatile, it may not be suitable for high-stress environments or applications involving aggressive chemicals.
Aluminum fittings offer lightweight options, making them ideal for applications where weight is a critical factor, such as in mobile equipment. However, aluminum fittings may not have the same durability as stainless steel or brass, especially in high-pressure situations.
In recent years, manufacturers have also begun exploring advanced materials like high-strength polymers and composites. These materials can provide unique benefits, such as reduced weight and enhanced resistance to corrosion. As technology advances, the development of innovative materials for hydraulic fittings is expected to expand, offering new solutions for diverse applications.
Material | Benefits | Limitations |
---|---|---|
Stainless Steel | Excellent corrosion resistance | Higher cost |
Brass | Cost-effective, good corrosion resistance | Limited use in aggressive environments |
Aluminum | Lightweight, suitable for low pressure | Lower durability under high stress |
3. How Do Environmental Conditions Affect Material Selection?
Environmental conditions significantly influence material selection for hydraulic fittings. This is where it gets interesting—understanding how factors like temperature, humidity, and chemical exposure impact material performance is crucial for making the right choices.
Temperature plays a critical role in material behavior. Extreme heat can cause materials to expand, while cold temperatures can lead to contraction. For hydraulic fittings exposed to high temperatures, materials must be selected for their ability to maintain integrity under such conditions. For instance, in industrial applications where fittings encounter high heat, materials like stainless steel are often preferred for their stability and strength.
Humidity and moisture are also vital considerations. Environments where fittings are exposed to water or moisture, such as marine applications, demand materials with high corrosion resistance. Stainless steel and specialized coatings can help prevent degradation and extend the lifespan of fittings in these conditions.
Chemical exposure is another essential factor in material selection. Hydraulic fittings may come into contact with various fluids, including oils and aggressive chemicals. Selecting materials that provide high resistance to these substances is critical to maintaining the integrity of the fittings and preventing premature failure.
By considering these environmental factors, procurement professionals can ensure that the hydraulic fittings they select will perform reliably and safely throughout their service life.
Environmental Factor | Impact on Material | Material Selection Considerations |
---|---|---|
Temperature | Affects expansion and contraction | Choose fittings rated for specific temperature ranges |
Chemical Exposure | Can degrade materials | Select materials with high chemical resistance |
Location | Outdoor conditions may cause damage | Use outdoor-rated fittings |
4. What Role Does Pressure Rating Play in Material Selection?
Pressure rating is a fundamental aspect of hydraulic fitting quality that significantly influences material selection. Ready for the good part? Understanding pressure ratings helps ensure that the fittings you choose can safely handle the demands of your hydraulic system.
Each hydraulic fitting is assigned a pressure rating that indicates the maximum pressure it can withstand without failing. This rating is critical for applications where hydraulic systems operate under high pressures. Materials used in the manufacturing of fittings must be capable of withstanding these pressures without deforming or rupturing.
When sourcing hydraulic fittings, it is essential to match the pressure rating of the fittings with the requirements of your hydraulic system. For example, if your system operates at a maximum pressure of 3000 psi, it is vital to select fittings rated above this threshold to provide a safety margin. Using fittings with inadequate pressure ratings can lead to catastrophic failures, resulting in leaks, equipment damage, and potential safety hazards.
Different materials exhibit varying strengths under pressure. For instance, stainless steel fittings generally have higher pressure ratings than brass fittings due to their superior tensile strength. Understanding the material properties and their pressure ratings is crucial for making informed procurement decisions.
Furthermore, it is important to consider not only the static pressure but also the dynamic pressures that may occur during operation. Hydraulic systems may experience pressure surges or spikes that exceed normal operating conditions. Choosing fittings that can withstand these potential pressure fluctuations is essential for ensuring the overall reliability and safety of the system.
Pressure Rating | Definition | Importance |
---|---|---|
Maximum Allowable Pressure | Highest pressure a fitting can handle | Prevents leaks and failures |
Burst Pressure | Pressure at which a fitting fails | Indicates safety limits |
Working Pressure | Normal operating pressure | Guides selection of appropriate fittings |
5. Why Is Corrosion Resistance Critical for Hydraulic Fittings?
Corrosion resistance is a vital quality indicator for hydraulic fittings. What’s the real story? The ability of a fitting to resist corrosion directly impacts its performance, longevity, and safety in hydraulic systems.
Hydraulic fittings are often exposed to various environmental conditions, including moisture, chemicals, and temperature fluctuations. These factors can contribute to the development of corrosion, which can weaken fittings and lead to leaks or failures. For instance, in marine applications, fittings are exposed to saltwater, which is particularly corrosive. Fittings made from materials with high corrosion resistance, such as stainless steel, are essential in these environments to ensure long-lasting performance and reliability.
The consequences of using fittings that lack adequate corrosion resistance can be severe. Corroded fittings can fail under pressure, leading to significant safety hazards and costly downtime. In industrial settings, such failures can halt production and result in expensive repairs. Therefore, investing in high-quality, corrosion-resistant fittings is crucial for maintaining system integrity and safety.
To combat corrosion, many manufacturers apply protective coatings to fittings. These coatings can enhance the corrosion resistance of materials and extend the lifespan of hydraulic components. When selecting fittings, it is essential to consider not only the base material but also any protective coatings that may be applied.
Ultimately, prioritizing corrosion resistance in hydraulic fittings can lead to improved reliability, reduced maintenance costs, and enhanced safety in hydraulic systems.
Material | Corrosion Resistance | Common Applications |
---|---|---|
Stainless Steel | Excellent resistance | Marine and chemical applications |
Brass | Good resistance | General-purpose applications |
Coated Aluminum | Enhanced resistance | Low-pressure systems with potential exposure |
6. How Does Cost Influence Material Selection?
Cost is a significant factor that influences material selection in hydraulic fitting procurement. This is where it gets interesting—while it may be tempting to choose the cheapest option, selecting fittings based solely on price can lead to long-term challenges.
High-quality materials often come with a higher upfront cost, but they can provide substantial long-term savings. For example, investing in stainless steel fittings may seem expensive initially, but their durability and corrosion resistance can translate into reduced maintenance and replacement costs over time. In contrast, opting for lower-cost brass fittings may lead to frequent failures, resulting in higher overall expenses.
When considering cost, it’s essential to evaluate the total cost of ownership rather than just the initial purchase price. This includes factors such as maintenance costs, potential downtime due to failures, and the lifespan of the fittings. A comprehensive cost analysis can help procurement professionals make informed decisions that align with their budget while ensuring quality.
Additionally, the choice of materials can also affect the overall efficiency of hydraulic systems. High-quality fittings that perform reliably can enhance system productivity, ultimately leading to better profitability. Therefore, while cost is an important consideration, it should not come at the expense of quality and reliability.
Cost Factor | Description | Long-Term Benefit |
---|---|---|
Initial Purchase Price | Upfront cost of fittings | Higher quality often leads to long-term savings |
Maintenance Costs | Expenses related to upkeep | Quality fittings require less maintenance |
Downtime Costs | Financial impact of system failures | Reliable fittings reduce downtime |
7. What Testing Methods Ensure Material Quality?
Testing methods are crucial for assessing the quality of materials used in hydraulic fittings. What’s the catch? Ensuring that materials meet performance standards through rigorous testing is essential for maintaining the safety and reliability of hydraulic systems.
One of the most common testing methods is tensile strength testing. This method measures the material’s ability to withstand tension and determines its maximum load capacity. Fittings that do not meet the required tensile strength may fail under pressure, leading to catastrophic failures in hydraulic systems.
Pressure testing is another critical method used to assess the integrity of hydraulic fittings. This involves subjecting fittings to pressures greater than their rated maximum to check for leaks or weaknesses. Pressure testing helps identify potential issues before installation, ensuring that only reliable fittings are used in hydraulic applications.
Additionally, corrosion resistance testing evaluates how well a material can withstand corrosive environments. This testing is particularly important for fittings that will be used in harsh conditions, such as marine or chemical processing applications. Materials that pass corrosion resistance tests are more likely to perform reliably over time, reducing the risk of leaks and failures.
By implementing comprehensive testing methods, manufacturers can ensure that their hydraulic fittings meet the necessary quality standards. This commitment to quality not only enhances the performance of hydraulic systems but also builds trust among customers and end-users.
Testing Method | Purpose | Importance |
---|---|---|
Tensile Strength Testing | Measures material load capacity | Ensures fittings can handle pressure |
Pressure Testing | Assesses integrity under pressure | Prevents leaks and identifies weaknesses |
Corrosion Resistance Testing | Evaluates durability in corrosive environments | Ensures long-lasting performance |
8. How Can You Evaluate Supplier Material Quality?
Evaluating the quality of materials supplied for hydraulic fittings is essential for ensuring that you source reliable components. So, how do you assess supplier material quality? Here are some effective strategies.
First, research the supplier’s reputation in the industry. A supplier with a long history and positive reviews is more likely to provide high-quality materials. Look for testimonials and case studies from other customers to gauge their experiences with the supplier. This can provide valuable insights into the reliability and quality of the materials offered.
Next, check for certifications and compliance with industry standards. Reputable suppliers should have certifications that demonstrate their commitment to quality, such as ISO or SAE certifications. These certifications indicate that the materials have been tested and meet established performance standards.
Additionally, consider conducting site visits to the supplier’s facilities if feasible. A firsthand look at the supplier’s operations can provide insights into their manufacturing processes, quality control measures, and overall capabilities. This due diligence can help ensure that you are partnering with a supplier that prioritizes material quality.
Finally, establish clear communication with the supplier regarding your quality expectations. Discuss your specific needs and requirements, and ensure that they understand the importance of delivering high-quality materials for hydraulic fittings. Strong communication fosters trust and can lead to better collaboration in the procurement process.
Evaluation Method | Description | Benefit |
---|---|---|
Supplier Research | Investigate supplier reputation and history | Indicates reliability and quality |
Certification Verification | Check for adherence to industry standards | Ensures compliance and quality assurance |
Site Visits | Assess manufacturing processes and quality control | Provides insight into supplier capabilities |
9. What Are the Common Mistakes to Avoid When Sourcing Fittings?
When sourcing hydraulic fittings, there are several common mistakes that can lead to costly issues. Understanding these pitfalls is essential for making informed decisions. What’s the catch? By avoiding these mistakes, you can enhance the reliability of your hydraulic systems.
One significant mistake is focusing solely on price rather than quality. While it may be tempting to choose the cheapest options, low-quality fittings can lead to failures and increased maintenance costs. Always prioritize quality indicators such as material, dimensional accuracy, and certifications over price alone.
Another common error is neglecting to verify supplier credentials. Failing to conduct due diligence on suppliers can result in sourcing substandard fittings. Ensure that you research suppliers thoroughly, looking for reviews, certifications, and industry reputation before making a purchase.
Ignoring compatibility is another mistake that can have severe consequences. When fittings are incompatible with hoses, pipes, or other components, it can lead to leaks and system failures. Always confirm that the fittings you choose meet the specifications required for your hydraulic system.
Finally, many professionals overlook the importance of maintaining clear records of fittings used in their systems. Keeping documentation of fitting specifications, certifications, and maintenance history is crucial for ensuring compliance and tracking performance over time.
Common Mistake | Description | Consequence |
---|---|---|
Focusing on Price | Selecting fittings based solely on cost | Increased maintenance costs and failures |
Neglecting Supplier Verification | Failing to research supplier credentials | Sourcing substandard fittings |
Ignoring Compatibility | Not confirming fitting specifications | Leaks and system failures |
10. How to Implement a Quality Assurance Process for Sourcing?
Implementing a quality assurance process for sourcing hydraulic fittings is essential for ensuring that your components meet the necessary standards. What’s the real story? A well-defined quality assurance process can help you maintain high-quality standards and reduce the risk of failures.
Start by creating a quality assurance checklist that outlines the key quality indicators you will evaluate when sourcing fittings. This checklist should include items such as material quality, dimensional accuracy, pressure ratings, surface finish, and certifications. Having a clear set of criteria will guide your sourcing decisions and help ensure consistency.
Next, establish relationships with reputable suppliers who prioritize quality. Communicate your quality standards and expectations to suppliers, and verify that they can meet these requirements. Regularly review supplier performance and provide feedback to ensure ongoing compliance with your quality assurance process.
Additionally, consider conducting regular audits of your sourcing process. Evaluate how well your quality assurance measures are being implemented and identify areas for improvement. This proactive approach will help you maintain high standards and ensure that your hydraulic systems operate reliably.
Finally, train your team on the importance of quality assurance in sourcing fittings. Ensure that all personnel involved in the sourcing process understand the quality indicators and the significance of adhering to them. This training will foster a culture of quality within your organization.
Quality Assurance Step | Description | Importance |
---|---|---|
Create Checklist | Outline key quality indicators | Guides sourcing decisions |
Establish Supplier Relationships | Ensure quality standards are met | Maintains consistent quality |
Conduct Audits | Evaluate sourcing process effectiveness | Identifies areas for improvement |
11. What Are the Benefits of Using High-Quality Hydraulic Fittings?
Investing in high-quality hydraulic fittings offers numerous benefits that can enhance the overall efficiency and reliability of hydraulic systems. So, what’s the scoop? Understanding these benefits can motivate you to prioritize quality in your sourcing decisions.
First, high-quality fittings are more durable and resistant to wear and tear. This durability leads to fewer failures and lower maintenance costs over time. In high-pressure applications, reliable fittings can prevent leaks, contributing to overall system efficiency and reducing the risk of catastrophic failures.
Moreover, using quality fittings enhances safety in hydraulic systems. Low-quality fittings are more likely to fail under pressure, posing risks to operators and equipment. High-quality fittings undergo rigorous testing and comply with industry standards, providing assurance that they will perform safely and effectively.
Additionally, high-quality fittings can improve system performance. When fittings are designed and manufactured to meet strict specifications, they facilitate better flow and pressure management within hydraulic systems. This improved performance can lead to enhanced productivity and operational efficiency.
Finally, investing in high-quality fittings contributes to long-term cost savings. Although the initial investment may be higher, the reduced maintenance and repair costs, combined with increased system reliability, ultimately lead to significant savings over time.
Benefit | Description | Impact |
---|---|---|
Durability | Fewer failures and lower maintenance costs | Increases system reliability |
Safety | Reduced risk of catastrophic failures | Protects operators and equipment |
Performance | Improved flow and pressure management | Enhances productivity |
12. How Do Environmental Factors Affect Fitting Quality?
Environmental factors play a significant role in determining the quality and performance of hydraulic fittings. This is where it gets interesting—considering these factors is essential for ensuring that fittings perform reliably under various conditions.
Temperature fluctuations can significantly impact hydraulic fittings. Extreme temperatures can cause materials to expand or contract, affecting the integrity of the fittings. For example, in applications where fittings are exposed to high heat, such as in industrial machinery, materials must be chosen for their ability to withstand elevated temperatures without compromising performance.
Humidity and moisture levels are also vital factors. In environments where fittings are exposed to water or moisture, such as marine applications, materials with high corrosion resistance, like stainless steel, are essential to prevent degradation. Corrosion can lead to leaks and failures, resulting in costly repairs and system downtimes.
Chemical exposure is another critical aspect of environmental considerations. Hydraulic fittings often operate in environments where they may be exposed to aggressive chemicals, oils, or other corrosive substances. Selecting materials that offer high resistance to these chemicals is essential for maintaining the integrity of the fittings and preventing premature failure.
Understanding the specific environmental conditions in which hydraulic fittings will operate is crucial for selecting the appropriate materials. By considering these factors, procurement professionals can ensure that the fittings will perform reliably and safely throughout their service life.
Environmental Factor | Impact on Material | Material Selection Considerations |
---|---|---|
Temperature | Affects expansion and contraction | Choose fittings rated for specific temperature ranges |
Chemical Exposure | Can degrade materials | Select materials with high chemical resistance |
Location | Outdoor conditions may cause damage | Use outdoor-rated fittings |
13. What Innovations Are Shaping the Future of Hydraulic Fittings?
The hydraulic fitting industry is constantly evolving, with new innovations emerging to enhance performance and safety. What’s the scoop? Staying informed about these innovations can give you a competitive edge in your operations.
One of the most significant trends is the development of advanced materials for hydraulic fittings. Manufacturers are increasingly using high-strength polymers and composites that offer superior corrosion resistance and reduced weight. These materials can improve the performance of hydraulic systems, especially in demanding environments where traditional metals may fail.
Another important innovation is the integration of smart technology into hydraulic fittings. Smart fittings equipped with sensors can monitor pressure, temperature, and fluid levels in real-time. This data can be invaluable for optimizing system performance and enabling proactive maintenance, ultimately reducing the risk of failures.
Additionally, there is a growing emphasis on sustainability in the hydraulic fitting industry. Manufacturers are adopting environmentally friendly practices, such as using recyclable materials and reducing waste during production. This shift not only benefits the environment but also aligns with the increasing demand for sustainable products in various industries.
Innovation | Description | Impact |
---|---|---|
Advanced Materials | Use of high-strength polymers and composites | Enhanced performance and corrosion resistance |
Smart Technology | Fittings with built-in sensors | Real-time monitoring for optimization |
Sustainability | Adoption of eco-friendly practices | Aligns with market demand for sustainable products |
14. How to Stay Informed About Quality Standards and Trends?
Staying informed about quality standards and trends in hydraulic fittings is essential for maintaining compliance and ensuring optimal performance. So, what are the best ways to keep up with industry developments?
One effective method is to subscribe to industry publications and newsletters. Many organizations, including ISO, SAE, and DIN, provide regular updates on changes to standards and best practices. These publications often feature articles, case studies, and expert insights that can enhance your understanding of the industry.
Another useful approach is to attend industry conferences and seminars. These events often feature presentations from experts who discuss the latest trends, technologies, and standards in hydraulic fittings. Networking with peers at these events can also provide valuable insights and resources.
Finally, consider joining professional associations related to hydraulic systems. Membership in these organizations often provides access to exclusive resources, including research papers, webinars, and training materials. Being part of a professional network can help you stay informed about changes in standards and connect with industry experts.
Information Source | Description | Benefit |
---|---|---|
Industry Publications | Subscribe to newsletters and journals | Stay updated on changes and best practices |
Conferences | Attend seminars and networking events | Gain insights from experts and peers |
Professional Associations | Join industry-related groups | Access exclusive resources and training |
15. What Are Common Questions About Hydraulic Fitting Standards?
As hydraulic fitting standards play a crucial role in the industry, it’s natural to have questions about their implications and applications. Here are some common inquiries professionals may have.
Understanding these questions can help clarify the significance of hydraulic fitting standards and their relevance to your operations.
Question | Answer |
---|---|
What are hydraulic fitting standards? | Hydraulic fitting standards are guidelines that ensure compatibility, safety, and reliability of hydraulic components. |
How does the ISO standard work? | The ISO standard provides specifications for hydraulic fittings, ensuring they meet certain safety and performance criteria for global compatibility. |
What is the SAE standard for hydraulic fittings? | The SAE standard outlines specifications and performance criteria for hydraulic fittings used primarily in automotive and industrial applications. |
What is the DIN standard for hydraulic fittings? | The DIN standard establishes technical specifications for hydraulic fittings, focusing on quality and compatibility within European markets. |
How do I choose the right standard for my application? | Consider factors such as system requirements, component compatibility, and consulting with industry experts to select the appropriate standard for your hydraulic fittings. |
Conclusion
In conclusion, understanding the importance of material selection in hydraulic fitting procurement is vital for ensuring the safety and efficiency of hydraulic systems. By focusing on key quality indicators such as material properties, pressure ratings, and environmental factors, procurement professionals can make informed decisions that enhance the reliability of their hydraulic systems. Prioritizing quality not only improves performance but also contributes to long-term cost savings and operational efficiency. Stay informed about innovations and industry standards to ensure your sourcing decisions align with best practices.
FAQ Section
Q1: What is material selection in hydraulic fitting procurement?
Material selection refers to the process of choosing appropriate materials for hydraulic fittings based on performance requirements and environmental conditions.
Q2: How does pressure rating affect material selection?
Pressure rating determines the maximum pressure a fitting can withstand, and different materials offer varying levels of strength and durability under pressure.
Q3: Why is corrosion resistance critical for hydraulic fittings?
Corrosion can significantly degrade fitting performance and lead to leaks, so selecting materials with high corrosion resistance is essential for long-lasting reliability.
Q4: What testing methods ensure material quality?
Common testing methods include tensile strength tests, pressure tests, and corrosion resistance evaluations, ensuring materials meet necessary specifications.
Q5: How can you evaluate supplier material quality?
Supplier material quality can be assessed by examining certifications, conducting audits, and reviewing historical performance and customer feedback.