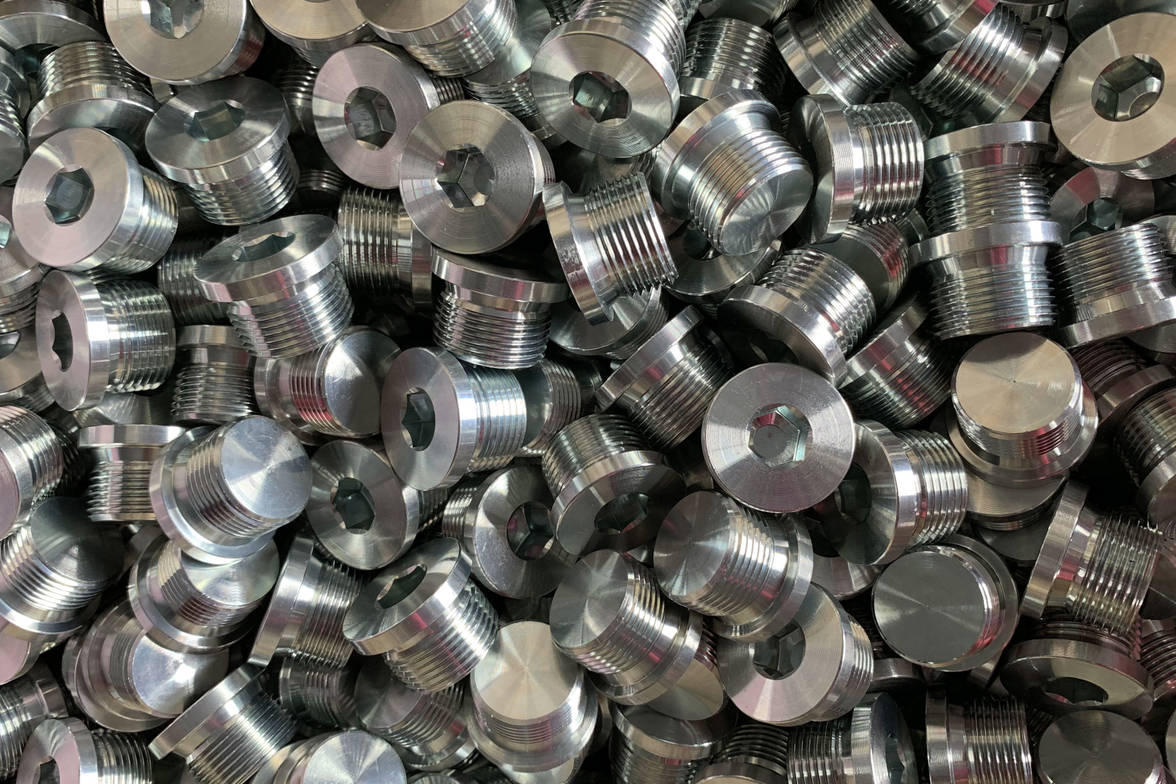
Understanding hydraulic fitting standards is crucial for professionals working with hydraulic systems. This article will provide a detailed exploration of the three primary standards: ISO, SAE, and DIN. We will delve into their significance, applications, and key differences. By the end of this article, you will gain insights into how these standards impact your choices and the overall efficiency of hydraulic systems.
1. What Are Hydraulic Fitting Standards?
Hydraulic fitting standards are established guidelines that dictate the specifications and performance expectations for hydraulic fittings. These standards are essential for ensuring that components are compatible and can safely withstand the pressures and conditions of hydraulic systems. But here’s the kicker—without these standards, the risk of leaks, failures, and unsafe operations would increase significantly.
The primary standards in hydraulic fittings are set by organizations such as the International Organization for Standardization (ISO), the Society of Automotive Engineers (SAE), and the Deutsches Institut für Normung (DIN). Each organization provides a set of criteria that manufacturers must adhere to when producing hydraulic fittings. This ensures that fittings are reliable and work effectively in various applications.
For instance, ISO standards focus on global compatibility, allowing fittings from different manufacturers to work together seamlessly. SAE standards are particularly influential in the automotive industry, ensuring that hydraulic components meet specific performance requirements. DIN standards are widely recognized in Europe, emphasizing quality and safety in hydraulic applications. Understanding these standards helps engineers and technicians select the right fittings for their systems, ultimately leading to better performance and safety.
Standard | Organization | Focus |
---|---|---|
ISO | International Organization for Standardization | Global compatibility |
SAE | Society of Automotive Engineers | Automotive applications |
DIN | Deutsches Institut für Normung | Quality and safety in Europe |
2. Why Are Hydraulic Fitting Standards Essential?
Hydraulic fitting standards are essential for several reasons. First and foremost, they ensure safety and reliability in hydraulic systems. What’s the real story? Without these standards, components could fail, leading to leaks or catastrophic system breakdowns.
By adhering to established standards, manufacturers can guarantee that their fittings will perform as intended under specified conditions. This is particularly important in high-pressure systems where the consequences of failure can be severe. For example, in industrial applications, a failure can result in equipment damage and pose safety risks to operators.
Moreover, hydraulic fitting standards promote compatibility among various components. When fittings are manufactured according to these standards, they can be used interchangeably across different brands and systems. This compatibility simplifies maintenance and repairs, allowing technicians to quickly replace or upgrade components without worrying about fitting mismatches.
Finally, standards help reduce the risk of system failures. By ensuring that all fittings meet rigorous performance criteria, companies can minimize downtime and maintenance costs. Investing in compliant fittings enhances the reliability of hydraulic systems, ultimately leading to improved productivity and operational efficiency.
Benefit | Explanation | Impact |
---|---|---|
Safety | Reduces risks of leaks and failures | Protects workers and equipment |
Compatibility | Ensures interchangeability of components | Simplifies maintenance and repairs |
Reliability | Minimizes downtime and maintenance costs | Enhances operational efficiency |
3. What Is the ISO Standard for Hydraulic Fittings?
The ISO standard for hydraulic fittings is one of the most recognized and widely adopted globally. ISO, or the International Organization for Standardization, develops standards that ensure compatibility and safety in hydraulic systems. This is where it gets interesting—ISO standards cover a wide range of specifications, making them essential for international trade and manufacturing.
ISO standards relevant to hydraulic fittings include ISO 8434, which specifies the requirements for metallic tube fittings. This standard ensures that fittings can reliably connect tubes in hydraulic systems without leaks. The ISO 16028 standard is also crucial as it pertains to quick connect under pressure couplings, allowing for fast and efficient connections in hydraulic applications.
Using ISO standards provides several benefits. First, it enhances global interoperability. When manufacturers produce fittings that comply with ISO standards, they can be used in hydraulic systems worldwide, facilitating international trade. This allows engineers to source components from various suppliers without compromising quality or performance.
Additionally, ISO standards help manufacturers improve their processes. By adhering to these guidelines, companies can implement best practices in design and production, resulting in higher-quality products. This commitment to quality not only boosts customer satisfaction but also enhances brand reputation in the competitive marketplace.
ISO Standard | Description | Application |
---|---|---|
ISO 8434 | Metallic tube fittings | Connecting tubes in hydraulic systems |
ISO 16028 | Quick connect couplings | Efficient connections under pressure |
4. What Is the SAE Standard for Hydraulic Fittings?
The SAE standard, established by the Society of Automotive Engineers, plays a significant role in the hydraulic fitting industry, particularly in North America. This standard focuses on providing specifications for hydraulic components, ensuring they meet the needs of automotive and industrial applications. Ready for the good part? Understanding SAE standards can help you choose the right fittings for your hydraulic systems.
One of the most important SAE standards is SAE J514, which covers the dimensions and performance of hydraulic tube fittings. This standard ensures that fittings are compatible with specific tube sizes and types, promoting seamless connections in hydraulic systems. Another key standard is SAE J1453, which addresses the requirements for threaded fittings, ensuring they can withstand high-pressure applications.
The benefits of using SAE standards are substantial. They provide a clear framework for manufacturers, ensuring that products are designed to meet specific performance criteria. This leads to higher quality and more reliable fittings, which is vital in industries where safety and efficiency are paramount.
Moreover, adhering to SAE standards fosters trust among customers and suppliers. When products are certified to meet these standards, engineers and technicians can be confident in their performance. This trust is essential for maintaining long-term relationships in the B2B sector, where reliability and quality are critical to success.
SAE Standard | Description | Focus Area |
---|---|---|
SAE J514 | Hydraulic tube fittings | Dimensions and performance |
SAE J1453 | Threaded fittings | High-pressure applications |
5. What Is the DIN Standard for Hydraulic Fittings?
The DIN standard, established by the Deutsches Institut für Normung, is another critical set of guidelines that governs hydraulic fittings, particularly in Europe. This standard is known for its rigorous requirements, ensuring that hydraulic components meet high quality and safety levels. What’s the catch? Understanding DIN standards is essential for anyone working with hydraulic systems in European markets.
DIN standards relevant to hydraulic fittings include DIN 2353, which specifies the dimensions and performance requirements for hydraulic tube fittings. This standard ensures that fittings are interchangeable and can withstand high pressures without failure. Another important standard is DIN 3861, covering the requirements for threaded fittings, which are commonly used in hydraulic applications.
By adhering to DIN standards, manufacturers can enhance the safety and reliability of their products. These standards require rigorous testing and quality assurance, ensuring that only the best fittings reach the market. This is crucial in industries such as manufacturing and construction, where the consequences of fitting failures can be severe.
Furthermore, DIN standards help facilitate international trade within Europe. When manufacturers produce fittings that comply with DIN requirements, they can easily market their products across different countries. This compatibility fosters trust among customers and suppliers, promoting smoother transactions and long-term relationships.
DIN Standard | Description | Application |
---|---|---|
DIN 2353 | Hydraulic tube fittings | Dimensions and performance |
DIN 3861 | Threaded fittings | High-pressure applications |
6. How Do ISO, SAE, and DIN Standards Compare?
When comparing ISO, SAE, and DIN standards, several key differences and similarities emerge. This is where it gets interesting—understanding these nuances can help you select the right fittings for your hydraulic systems.
ISO standards are recognized globally and focus on ensuring compatibility among components regardless of the manufacturer. This global perspective promotes international trade and collaboration. In contrast, SAE standards are primarily focused on the North American market, emphasizing automotive applications and performance specifications.
DIN standards, on the other hand, are widely adopted in Europe and prioritize high-quality and safety requirements. While DIN standards also aim for compatibility, they are more rigorous in terms of testing and certification processes. This can lead to a higher assurance of quality but may also result in longer lead times for product development.
One significant similarity among these standards is their commitment to safety and reliability. All three organizations emphasize the importance of producing fittings that can withstand high pressures and harsh conditions. This shared focus ensures that engineers and technicians can trust the products they select, regardless of the standard they choose.
Standard | Focus | Market |
---|---|---|
ISO | Global compatibility | International |
SAE | Automotive performance | North America |
DIN | Quality and safety | Europe |
7. How Do I Choose the Right Standard for My Application?
Choosing the right standard for your hydraulic fittings is crucial for ensuring optimal performance and safety. So, how do you make the best decision? Let’s break it down into manageable steps.
First, assess your specific application requirements. Consider factors such as pressure ratings, environmental conditions, and fluid types. For example, if you are working in a high-pressure environment, you may want to prioritize standards known for their rigorous testing, such as DIN or SAE.
Next, evaluate the components of your hydraulic system. If your system includes parts from different manufacturers, ISO standards may be the best choice to ensure compatibility. Additionally, if you are operating primarily in North America, SAE standards could be more appropriate due to their focus on automotive applications.
Consulting with industry experts is also a valuable step in the decision-making process. Engineers and technicians with experience in hydraulic systems can provide insights into which standards are most commonly used in similar applications. They can also help you understand the implications of choosing one standard over another.
Finally, consider the availability of components that meet the chosen standards. Selecting a standard that has widespread industry adoption will make sourcing fittings easier and more cost-effective.
Consideration | Description | Importance |
---|---|---|
Application Requirements | Assess pressure and environment | Ensures optimal performance |
Component Compatibility | Evaluate parts from different manufacturers | Promotes seamless integration |
Expert Consultation | Seek insights from experienced professionals | Informs decision-making |
8. What Are the Implications of Non-Compliance with Standards?
Non-compliance with hydraulic fitting standards can have serious implications for businesses. What’s the catch? Understanding these risks can help you avoid costly mistakes and ensure the safety and reliability of your hydraulic systems.
One of the primary risks associated with non-compliance is the potential for system failures. Using fittings that do not meet established standards can lead to leaks, pressure drops, and catastrophic failures, which can result in significant downtime and repair costs. For example, a hydraulic system failure in a manufacturing plant can halt production, leading to lost revenue and missed deadlines.
Additionally, non-compliance can expose businesses to legal liabilities. If an accident occurs due to the use of substandard fittings, companies may face lawsuits from injured parties or regulatory fines. This legal exposure can damage a company’s reputation and lead to increased insurance premiums.
Moreover, using non-compliant fittings can affect the overall quality of operations. When components do not meet industry standards, the performance of the entire hydraulic system may suffer. This can lead to inefficiencies, increased maintenance costs, and a lack of trust among customers.
Implication | Description | Consequence |
---|---|---|
System Failures | Risk of leaks and breakdowns | Downtime and repair costs |
Legal Liabilities | Exposure to lawsuits and fines | Damage to reputation and increased premiums |
Operational Quality | Reduced performance and efficiency | Higher maintenance costs |
9. How Can I Ensure My Fittings Meet Industry Standards?
Ensuring that your hydraulic fittings meet industry standards is essential for maintaining safety and reliability. So, what steps can you take to verify compliance? Let’s explore effective strategies to ensure your fittings adhere to the necessary standards.
First, source fittings from reputable manufacturers. Companies that have a history of producing high-quality hydraulic components are more likely to comply with industry standards. Look for manufacturers that provide certifications and documentation to prove compliance with ISO, SAE, or DIN standards.
Next, conduct thorough inspections of all fittings before installation. Check for visible defects, such as cracks or corrosion, and ensure that the fittings are labeled with the appropriate certifications. This step is crucial for identifying potential issues before they lead to system failures.
Additionally, keep detailed records of all fittings used in your hydraulic systems. This documentation should include information about the manufacturer, certification, and installation date. By maintaining accurate records, you can easily track the compliance status of your fittings and ensure timely replacements when necessary.
Finally, consider conducting regular audits of your hydraulic systems. Engaging a third-party inspector to evaluate compliance with industry standards can provide an unbiased assessment and help identify areas for improvement.
Verification Method | Description | Benefit |
---|---|---|
Sourcing | Choose reputable manufacturers | Higher likelihood of compliance |
Inspections | Check for defects and certifications | Prevents installation of substandard fittings |
Record Keeping | Maintain detailed fitting documentation | Facilitates compliance tracking |
10. What Are the Latest Trends in Hydraulic Fitting Standards?
The hydraulic fitting industry is constantly evolving, with new trends and technologies emerging to enhance performance and safety. What’s the scoop? Staying informed about these trends can give you a competitive edge in your operations.
One of the latest trends is the increasing use of advanced materials in hydraulic fittings. Manufacturers are exploring high-strength polymers and composites that offer superior corrosion resistance and reduced weight. These materials can enhance the performance of hydraulic systems, particularly in demanding environments where traditional metals may fail.
Another significant trend is the integration of smart technology into hydraulic fittings. Smart fittings equipped with sensors can monitor pressure, temperature, and fluid levels in real-time. This data can be invaluable for optimizing system performance and enabling proactive maintenance, ultimately reducing the risk of failures.
Additionally, there is a growing emphasis on sustainability in the hydraulic fitting industry. Manufacturers are adopting environmentally friendly practices, such as using recyclable materials and reducing waste during production. This shift not only benefits the environment but also aligns with the increasing demand for sustainable products in various industries.
Trend | Description | Impact |
---|---|---|
Advanced Materials | Use of high-strength polymers and composites | Enhanced performance and corrosion resistance |
Smart Technology | Fittings with built-in sensors | Real-time monitoring for optimization |
Sustainability | Adoption of eco-friendly practices | Aligns with market demand for sustainable products |
11. How Do Environmental Factors Affect Fitting Standards?
Environmental factors significantly influence the performance and longevity of hydraulic fittings. So, what should you consider regarding the environment in which your fittings will operate?
Temperature variations can affect hydraulic fittings in various ways. Extreme heat can cause materials to expand, while cold temperatures may lead to contraction. This can compromise the integrity of the fittings, potentially resulting in leaks or failures. Selecting fittings designed to withstand specific temperature ranges is essential for maintaining system reliability.
Additionally, exposure to chemicals and contaminants can degrade the performance of hydraulic fittings. In industries such as agriculture or manufacturing, fittings may encounter corrosive substances that can damage materials. Choosing fittings with appropriate chemical resistance ratings is vital to ensure they can withstand the specific conditions of your operating environment.
Furthermore, the location of your hydraulic systems plays a crucial role in fitting selection. Outdoor applications may expose fittings to harsh weather conditions, such as rain, snow, or UV radiation. Using fittings designed for outdoor use can help mitigate these risks and extend the lifespan of your hydraulic components. Assessing the environmental factors affecting your fittings is essential for making informed choices.
Environmental Factor | Impact | Consideration |
---|---|---|
Temperature | Affects material integrity | Choose fittings rated for temperature variations |
Chemical Exposure | Can degrade materials | Select fittings with chemical resistance |
Location | Outdoor conditions may cause damage | Use outdoor-rated fittings |
12. What Role Do Manufacturers Play in Compliance?
Manufacturers play a pivotal role in ensuring compliance with hydraulic fitting standards. This is where it gets interesting—understanding their responsibilities can help you make informed decisions about the components you use in your systems.
One of the primary responsibilities of manufacturers is to produce fittings that meet established industry standards. This involves rigorous testing and quality assurance processes to ensure that products perform as expected under specified conditions. Manufacturers must also stay updated on changes to standards and regulations to maintain compliance.
Additionally, manufacturers are responsible for providing accurate documentation and certification for their products. This documentation is crucial for customers who need to verify that the fittings meet the necessary standards. By providing clear and transparent information, manufacturers can build trust with their customers and enhance their reputation in the market.
Finally, manufacturers should offer support and guidance to customers regarding compliance. This includes providing resources on how to properly install and maintain fittings to ensure they continue to meet standards over time. Educating customers about the importance of compliance can help prevent issues and ensure safe and reliable operations.
Manufacturer Responsibility | Description | Importance |
---|---|---|
Product Compliance | Produce fittings meeting industry standards | Ensures safety and reliability |
Documentation | Provide certification and product information | Facilitates customer trust |
Customer Support | Offer guidance on installation and maintenance | Prevents compliance issues |
13. How Can I Stay Informed About Changes in Standards?
Staying informed about changes in hydraulic fitting standards is essential for maintaining compliance and ensuring optimal performance. So, what are the best ways to keep up with industry developments?
One effective method is to subscribe to industry publications and newsletters. Many organizations, including ISO, SAE, and DIN, provide regular updates on changes to standards and best practices. These publications often feature articles, case studies, and expert insights that can enhance your understanding of the industry.
Another useful approach is to attend industry conferences and seminars. These events often feature presentations from experts who discuss the latest trends, technologies, and standards in hydraulic fittings. Networking with peers at these events can also provide valuable insights and resources.
Finally, consider joining professional associations related to hydraulic systems. Membership in these organizations often provides access to exclusive resources, including research papers, webinars, and training materials. Being part of a professional network can help you stay informed about changes in standards and connect with industry experts.
Information Source | Description | Benefit |
---|---|---|
Industry Publications | Subscribe to newsletters and journals | Stay updated on changes and best practices |
Conferences | Attend seminars and networking events | Gain insights from experts and peers |
Professional Associations | Join industry-related groups | Access exclusive resources and training |
14. How Do Standards Impact Hydraulic System Design?
Standards have a significant impact on hydraulic system design, influencing everything from component selection to overall system performance. What’s the real story? Understanding this impact can help you design more efficient and reliable hydraulic systems.
One key area where standards influence design is in component selection. When engineers design hydraulic systems, they must consider the specifications outlined by relevant standards. This ensures that all components, including fittings, hoses, and valves, are compatible and can function together effectively. Adhering to standards during the design phase reduces the risk of failures and enhances overall system reliability.
Moreover, standards can dictate the design process itself. Many manufacturers are required to follow specific guidelines during production to ensure compliance with industry standards. This can affect the choice of materials, manufacturing techniques, and quality control measures. By aligning design practices with standards, manufacturers can produce components that meet safety and performance expectations.
Finally, incorporating standards into the design process can facilitate system optimization. Engineers can leverage standardized components to create systems that are more efficient and easier to maintain. This optimization ultimately leads to improved operational performance and reduced costs over time.
Design Impact | Description | Benefit |
---|---|---|
Component Selection | Ensures compatibility and functionality | Reduces risk of failures |
Production Guidelines | Dictates manufacturing practices | Enhances safety and quality |
System Optimization | Facilitates use of standardized components | Improves efficiency and reduces costs |
15. What Are Common Questions About Hydraulic Fitting Standards?
As hydraulic fitting standards play a crucial role in the industry, it’s natural to have questions about their implications and applications. Here are some common inquiries professionals may have.
Understanding these questions can help clarify the significance of hydraulic fitting standards and their relevance to your operations.
Question | Answer |
---|---|
What are hydraulic fitting standards? | Hydraulic fitting standards are guidelines that ensure compatibility, safety, and reliability of hydraulic components. |
How does the ISO standard work? | The ISO standard provides specifications for hydraulic fittings, ensuring they meet certain safety and performance criteria for global compatibility. |
What is the SAE standard for hydraulic fittings? | The SAE standard outlines specifications and performance criteria for hydraulic fittings used primarily in automotive and industrial applications. |
What is the DIN standard for hydraulic fittings? | The DIN standard establishes technical specifications for hydraulic fittings, focusing on quality and compatibility within European markets. |
How do I choose the right standard for my application? | Consider factors such as system requirements, component compatibility, and consulting with industry experts to select the appropriate standard for your hydraulic fittings. |
Conclusion
In conclusion, understanding hydraulic fitting standards is vital for ensuring the safety and reliability of hydraulic systems. By exploring ISO, SAE, and DIN standards, you can make informed decisions that enhance your operations. Each standard serves a unique purpose, and adhering to these guidelines can help prevent costly failures and ensure optimal performance. Prioritize compliance, stay informed about changes, and leverage these standards to achieve greater efficiency and reliability in your hydraulic systems.
FAQ Section
Q1: What are hydraulic fitting standards?
Hydraulic fitting standards are guidelines that ensure compatibility, safety, and reliability of hydraulic components.
Q2: How does the ISO standard work?
The ISO standard provides specifications for hydraulic fittings, ensuring they meet certain safety and performance criteria for global compatibility.
Q3: What is the SAE standard for hydraulic fittings?
The SAE standard outlines specifications and performance criteria for hydraulic fittings used primarily in automotive and industrial applications.
Q4: What is the DIN standard for hydraulic fittings?
The DIN standard establishes technical specifications for hydraulic fittings, focusing on quality and compatibility within European markets.
Q5: How do I choose the right standard for my application?
Consider factors such as system requirements, component compatibility, and consulting with industry experts to select the appropriate standard for your hydraulic fittings.